ROTARY DRYER
Introduction
Application Field: Suitable for various industries such as Metallurgy, Building Materials, Light Industry, Chemical Industry and Casting Industry etc…
Processing Materials: Rotary dryer is often used to dry metal powder, iron concentrate pellets, blue carbon, lignite, fly ash, quartz sand, clay, limestone, slime, river sand, clay, iron oxide scale, sludge, coke, copper concentrate, silicon carbide powder, rare earth ore, mineral powder, tin ore powder, cobalt ore powder, nickel ore powder, manganese ore powder, gypsum powder, bentonite, kaolin, gold ore powder, iron ore powder, steel slag, fluorite ore, coal powder and mixed materials.
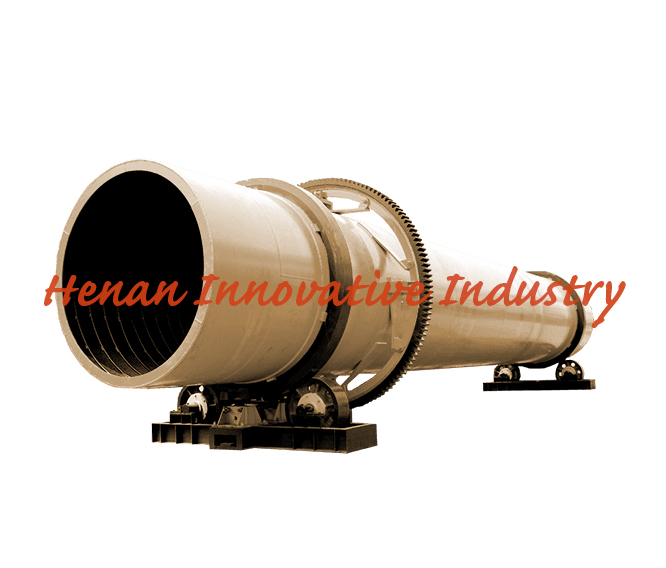
Production Capacity : 1.9 ~ 76 t/h
Shell Cubage : 9.0 ~ 285 m³
Weight : 9 ~ 135 t
Main Motor Power : 7.5 ~ 160 KW
The rotary dryer is a type of industrial dryer employed to reduce or minimize the liquid moisture content of the material it is handling by bringing it into direct contact with a heated gas.
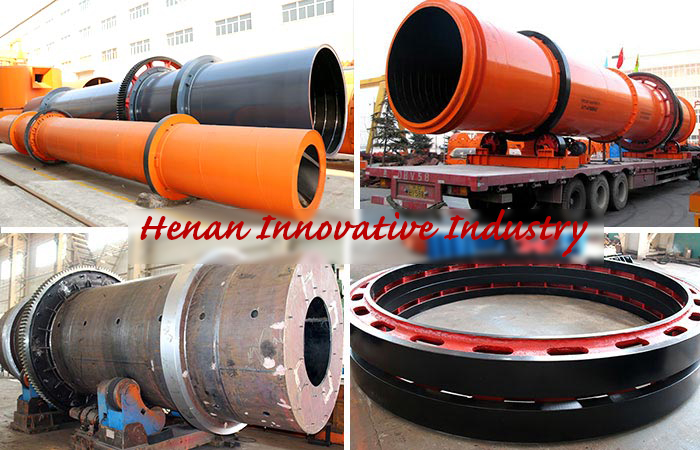
Rotary dryers are a highly efficient industrial drying option for bulk solids. They are often chosen for their robust processing capabilities and their ability to produce uniform results despite variance in feed-stock.
Rotary dryers work by tumbling material in a rotating drum in the presence of a drying air. They can also be indirectly heated to avoid direct contact between the material and processing medium.
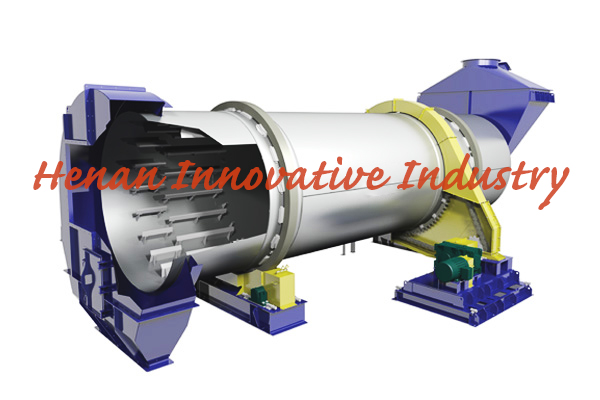
THE STRUCTURE AND WORKING PRINCIPLE OF ROTARY DRYER
The rotary dryer is mainly composed of a frame, a heat supply source, a loading machine, a feeding machine, a rotary drum, a material crushing device, a discharging machine, an induced draft fan, a dis-charger, and a power distribution cabinet.
The dryer is made up of a large, rotating cylindrical tube, usually supported by concrete columns or steel beams. The dryer is inclined to slopes slightly so that the discharge end is lower than the material feed end in order to convey the material through the dryer under gravity.
Material which needs to be dry enters the dryer, and as the dryer rotates, the material is lifted up by a series of internal fins lining on the inner wall of the dryer. When the material gets high enough to roll back off the fins, it falls back down to the bottom of the dryer, passing through the hot gas stream as it falls.
This gas stream can either be moving toward the discharge end from the feed end (known as co-current flow), or toward the feed end from the discharge end (known as counter-current flow).
The gas stream can be made up of a mixture of air and combustion gases from a burner, in which case the dryer is called a direct heated dryer.
Alternatively, the gas stream may consist of air or another (sometimes inert) gas that is preheated. When the gas stream is preheated by some means where burner combustion gases do not enter the dryer, the dryer known as an indirect-heated type. Often, indirect heated dryers are used when product contamination is a concern. In some cases, a combination of direct-indirect heated rotary dryers are also available to improve the overall efficiency.
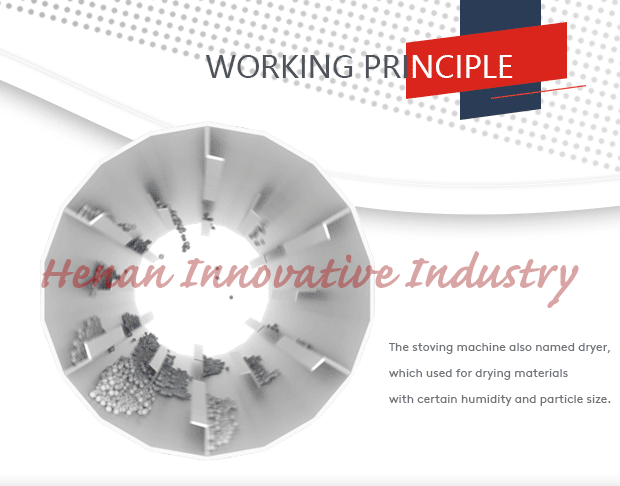
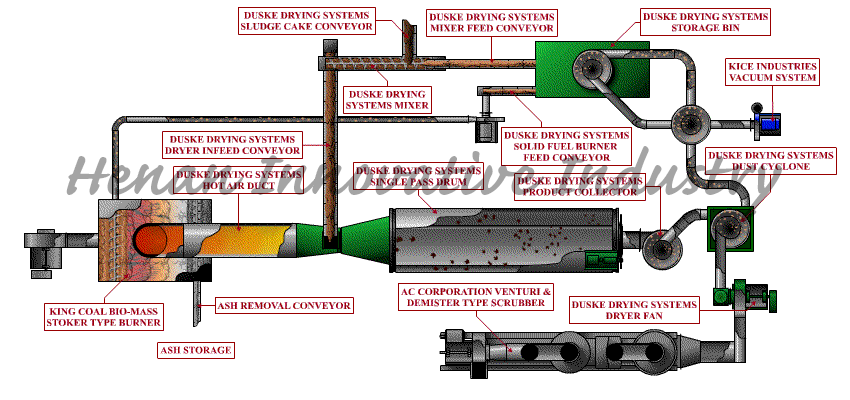
Bio-solids Management Solution
FEATURES AND ADVANTAGES
(1) Adopt gas generator, electric gas and combustor as heat source and supporting equipment has conveyor, hoister, dust removing device, and feeder. Rotary dryer is made up of feeding part, discharging part, rotary part, wind tunnel and reduction box and etc…
(2) Rotary dryer is used widely in various industries, and the color and shape of final product is very good. When the dryer is working, it keeps smooth and can dry material very fast, which obtains higher revenue.
(3) The Spiral conveyor has a simple structure, convenient maintenance and low cost.The rotary dryer can control the temperature of barrel, and we can install thermometer at the feeding part, so that we can control the temperature of materials.
(4) The moisture is controllable; Multi-channel intelligent anti-ignition; Reliable fire handling equipment; Coal & power saving, various heat sources can be used; Full automatic control & Pollution-free emission.
(5) Rotary dryers are less sensitive to particle size. It can accept the highest flue gasses of any type of dryer. Low maintenance cost; thus economical. It has the greatest capacity than any type of dryer.